Manufacturing Readiness Levels (MRLs)
What are Manufacturing Readiness Levels?
Manufacturing Readiness Levels (TRLs) are shorthand labels for pre-defined qualitative characterization of how mature are the manufacturing processes used to realize a given technology. They are not quantitative, 100%-objective measures of readiness, but instead represent a subjective, but expert, view of the current or future maturity of a given technology’s manufacturability.
INEMI’s approach to MRLs
The definitions used here are essentially those provided by USA’s Department of Defence (DOD)1 and subsequently modified by NextFlex.2 The changes are mainly deletions of references to formal processes used within the DOD.
MRL Definitions
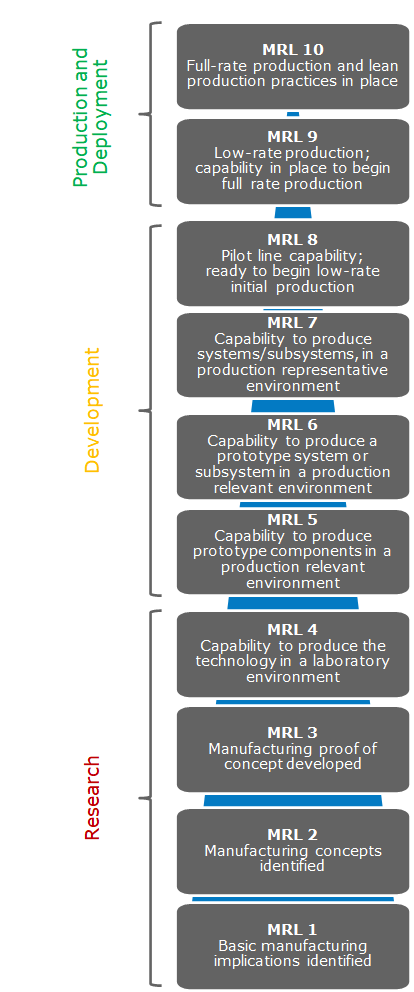
List of Manufacturing Readiness Levels (MRLs)
MRL 1: Basic Manufacturing Implications Identified
This is the lowest level of manufacturing readiness. Basic research is needed to address manufacturing shortfalls and opportunities needed to achieve program objectives.
MRL 2: Manufacturing Concepts Identified
This level is characterized by describing the application of new manufacturing concepts. Applied research translates basic research into solutions for broadly defined end-user needs. Typically, this level of readiness includes identification, paper studies and analysis of material and process approaches. An understanding of manufacturing feasibility and risk is emerging.
MRL 3: Manufacturing Proof of Concept Developed
This level begins the validation of the manufacturing concepts through analytical or laboratory experiments. This level of readiness is typical of technologies at the stages of applied research and advanced development. Materials and/or processes have been characterized for manufacturability and availability, but further evaluation and demonstration is required. Experimental hardware models have been developed in a laboratory environment that may possess limited functionality.
MRL 4: Capability to produce the technology in a laboratory environment
This level indicates that the technologies are ready for technology development. At this point, required investments, such as manufacturing technology development, have been identified. Processes to ensure manufacturability, producibility, and quality are in place and are sufficient to produce technology demonstrators. Manufacturing risks have been identified for building prototypes and mitigation plans are in place. Target cost objectives have been established and manufacturing cost drivers have been identified. Producibility assessments of design concepts have been completed. Key design performance parameters have been identified as well as any special tooling, facilities, material handling and skills required.
MRL 5: Capability to produce prototype components in a production relevant environment
The industrial base has been assessed to identify potential manufacturing sources. A manufacturing strategy has been refined and integrated with the risk management plan. Identification of enabling/critical technologies and components is complete. Prototype materials, tooling and test equipment, as well as personnel skills have been demonstrated on components in a production relevant environment, but many manufacturing processes and procedures are still in development. Manufacturing technology development efforts have been initiated or are ongoing. Producibility assessments of key technologies and components are ongoing. A cost model has been constructed to assess projected manufacturing cost.
MRL 6: Capability to produce a prototype system or subsystem in a production relevant environment
It is normally seen as the level of manufacturing readiness that denotes completion of technology development and acceptance into a preliminary system design. An initial manufacturing approach has been developed. The majority of manufacturing processes have been defined and characterized, but there are still significant engineering and/or design changes in the system itself. However, preliminary design of critical components has been completed and producibility assessments of key technologies are complete. Prototype materials, tooling and test equipment, as well as personnel skills have been demonstrated on systems and/or subsystems in a production relevant environment. A cost analysis has been performed to assess projected manufacturing cost versus target cost objectives and the program has in place appropriate risk reduction to achieve cost requirements or establish a new baseline. This analysis should include design trades. Producibility considerations have shaped system development plans. Long-lead and key supply chain elements have been identified.
MRL 7: Capability to produce systems, subsystems, or components in a production representative environment
System detailed design activity is underway. Material specifications have been approved and materials are available to meet the planned pilot line build schedule. Manufacturing processes and procedures have been demonstrated in a production representative environment. Detailed producibility trade studies and risk assessments are underway. The cost model has been updated with detailed designs, rolled up to system level, and tracked against allocated targets. Unit cost reduction efforts have been prioritized and are underway. The supply chain and supplier quality assurance have been assessed and long-lead procurement plans are in place. Production tooling and test equipment design and development have been initiated.
MRL 8: Pilot line capability demonstrated; Ready to begin Low-Rate Initial Production
This level is associated with entry into Low-Rate Initial Production (LRIP). Detailed system design is essentially complete and sufficiently stable to enter low-rate production. All materials are available to meet the planned low-rate production schedule. Manufacturing and quality processes and procedures have been proven in a pilot line environment and are under control and ready for low-rate production. Known producibility risks pose no significant challenges for low-rate production. The engineering cost model is driven by detailed design and has been validated with actual data. The supply chain is established and stable.
MRL 9: Low-rate production demonstrated; Capability in place to begin Full Rate Production
At this level, the system, component or item has been previously produced, is in production, or has successfully achieved low-rate initial production. This level of readiness is normally associated with readiness for entry into Full-Rate Production (FRP). All systems engineering/design requirements should have been met such that there are minimal system changes. Major system design features are stable and have been proven in test and evaluation. Materials are available to meet planned rate production schedules. Manufacturing process capability in a low-rate production environment is at an appropriate quality level to meet design key characteristic tolerances. Production risk monitoring is ongoing. LRIP cost targets have been met and learning curves have been with actual data. The cost model has been developed for FRP environment and reflects the impact of continuous improvement.
MRL 10: Full-Rate Production demonstrated and lean production practices in place
This is the highest level of production readiness. Engineering/design changes are few and generally limited to quality and cost improvements. System, components or items are in full-rate production and meet all engineering, performance, quality and reliability requirements. Manufacturing process capability is at the appropriate quality level. All materials, tooling, inspection and test equipment, facilities and manpower are in place and have met full-rate production requirements. Rate production unit costs meet goals, and funding is sufficient for production at required rates. Lean practices are well established and continuous process improvements are ongoing.
References
Department of Defence (USA), “DoD Manufacturing Readiness Levels,” http://www.dodmrl.com/.
NextFlex, “Manufacturing Raadiness Levels Definition,” https://www.nextflex.us/wp-content/uploads/NextFlex_OPC_MRL_TRL_Definitions.pdf.