Testability/In-Field Reliability for CIS
Importance of testability
The design and development of CIS often neglect a critical factor—testability—which influences yield, durability, and reliability. Unlike traditional chip packaging, diverse CIS designs lack standardized test protocols. For instance, LiDAR systems with laser diode arrays and tight tolerances or projection modules with wafer-level MEMS and active light sources present unique challenges. In contrast, camera modules typically involve a singular wafer-level sensor and lens assembly. Figure 1 illustrates considerations for test from design through deployment.
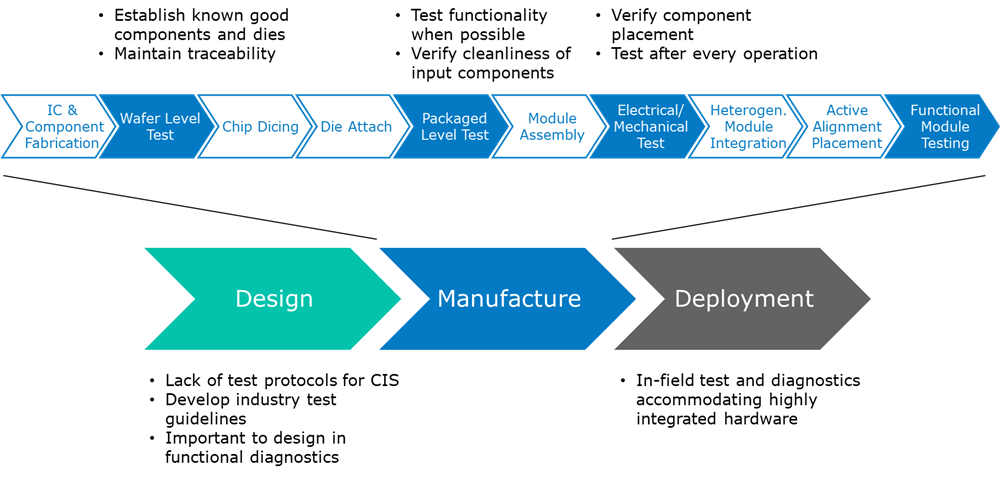
Figure 1. Test considerations for CIS.
Prioritization of early design for test
Given the cost implications of low yield at different stages of CIS manufacturing and the difficulty of re-work, prioritizing early design for test (DFT) and ensuring system reliability is crucial. This involves simulations (computer aided design (CAD), finite element analysis (FEA), and computational fluid dynamics (CFD), failure analysis), highly accelerated life testing/highly accelerated stress screening (HALT/HASS), and compliance with environmental standards like the American Society for Testing and Materials (ASTM), military standard (MIL-STD), and the Society of Automotive Engineers (SAE). In the absence of standard test protocols, as is often the case in high-mix manufacturing, implementing common guidelines and built-in functional diagnostics is essential.
Sub-assembly verification
As systems undergo miniaturization, component alignment becomes more challenging without designed fiducials or alignment features. CIS tends to move away from electrical interposers, opting for direct component placement onto mechanical substrates, often on different surfaces, maintaining micron tolerances in two to six axes.
Identifying known good CIS sub-assemblies prior to packaging is vital. Verification of component placement and testing before and after each operation is key to maintaining yields and production costs. Waiting until the end, assuming testing is done before a shift/batch may seem reasonable, but it is not advisable given the high labor, material, and facilities costs compared to standard products. In addition, maintaining traceability is a must, and while testing sub-assemblies might not be possible, measurements can ensure placement is within specifications, often facilitated by the precision placement pick-and-place equipment.
Early consideration of DFT, design for assembly (DFA), environmental reliability testing, and traceability is essential for enhancing the overall performance, durability, and reliability of CIS.
Return to topic overview