Advanced Driver Assistance Systems for Passenger Vehicles
The passenger vehicle camera sensor subsystems integrated in advanced driver assistance systems (ADAS) are projected to experience robust compound annual growth rates achieving revenues of $12B by 2030 for North America (NA), Europe, and China1. These subsystems are typically classified as 1) short/medium-range radar, 2) long-range radar, 3) exterior camera, 4) interior camera, and 5) light detection and ranging (LiDAR). These subsystems provide critical functionality such as 360° surround view, blind spot cross-traffic alert, pedestrian detection, and forward and rear collision warning.
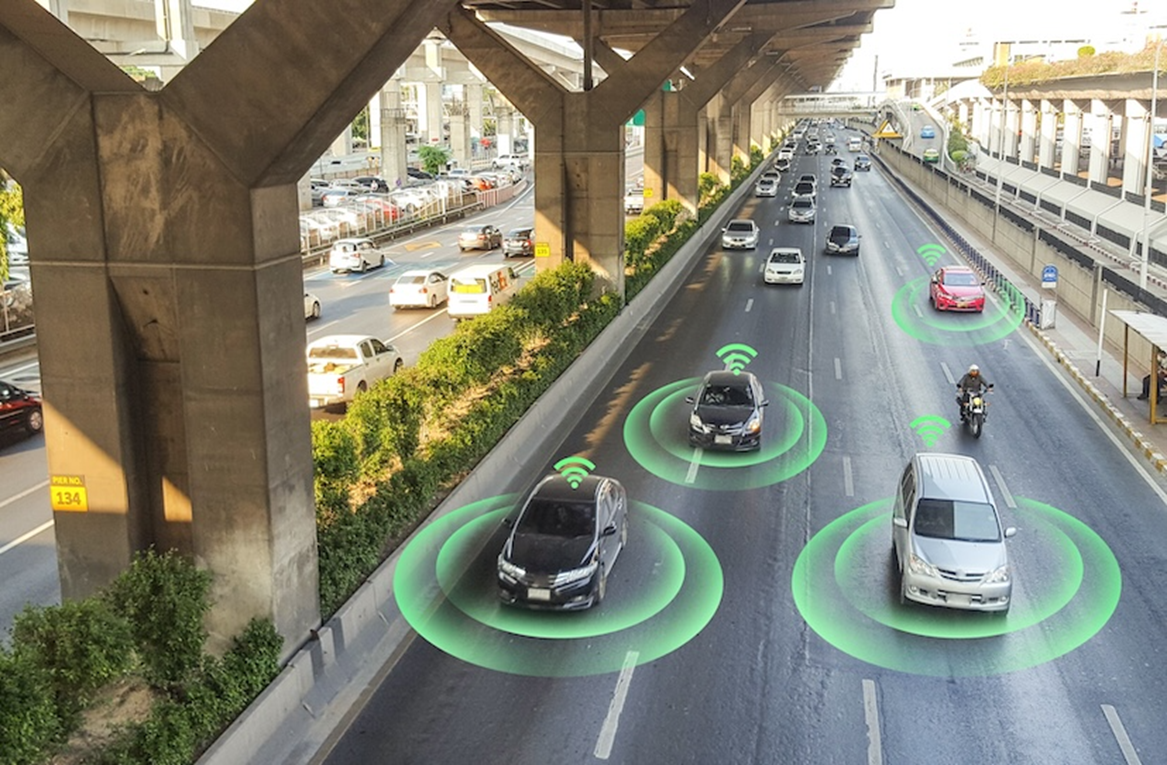
Figure 1. An ADAS implementation: LiDAR and other sensing systems combined with distributed, networked intelligence.
High-yield volume manufacturing of these subsystems is achieved by leveraging the complex integrated systems capabilities portfolio (design, materials, assembly, test, etc.). These capabilities must address the following challenges:
The performance of these subsystems is dependent on the ability to consistently achieve sub-5 µm automated precision placement (decreasing to 1 µm in the next decade) of optical and electro-mechanical components, as well as electronic integrated circuit (EIC) and photonic integrated circuit (PIC) devices.
The processing parameters for micro-volume metering, dispensing, and curing of materials providing optical, electrical, thermal, and structural properties must be tightly controlled to ensure reliable subsequent processing and reliable in-field subsystem operation.
These subsystems demand packaging materials and structural designs that enable operation in aggressive environments (e.g., temperature, humidity, liquids, vibration, impact). This additional requirement challenges the designers to select CIS technologies that have demonstrated long-term operation stability and subsystem ruggedization integrity.
Thorough cleaning of electronic assemblies is crucial for ADAS to maintain reliability and performance. Contaminants and flux residues left on assemblies can lead to electrical shorts, signal interference, and corrosion, compromising ADAS functionality.
This requires tightly controlling processing parameters, deploying both die- and wafer-level assembly equipment, using high-quality components, and a cleanroom manufacturing environment.
The continued customer adoption and integration of these subsystems in vehicles to offer enhanced situation awareness will accelerate CIS technology development and deployment.
Return to topic overview
References
Frost & Sullivan, https://www.frost.com/.